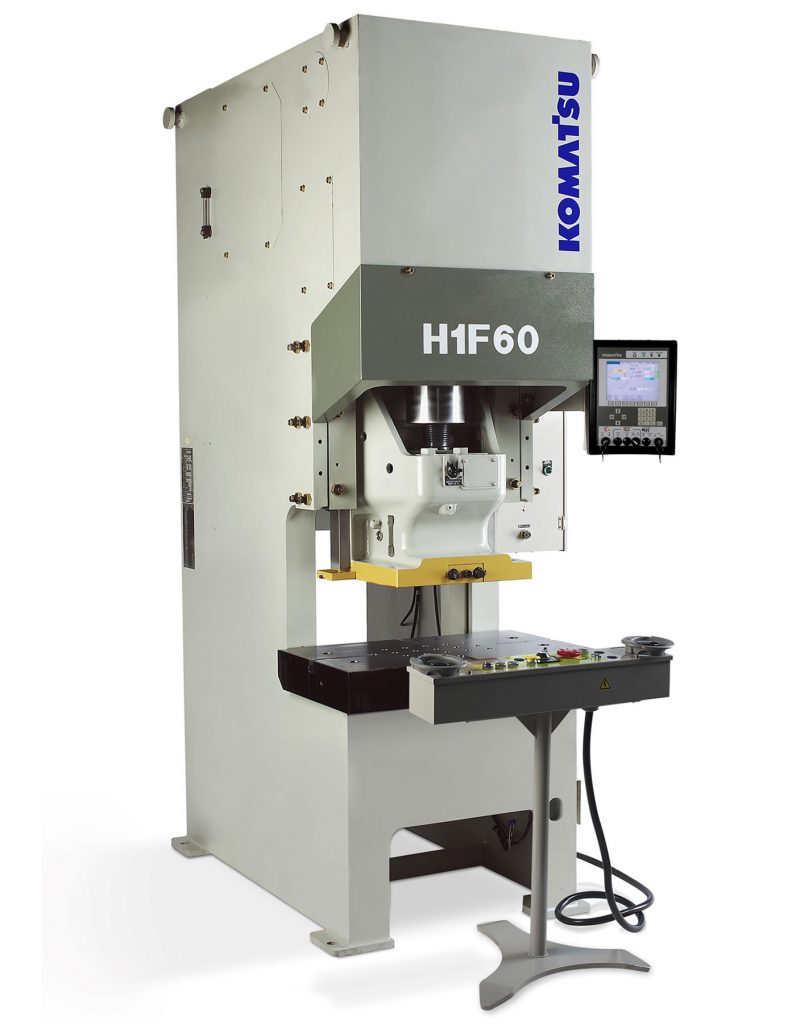
Servo Motions
Imagine, total control of slide velocity, multiple stroke depth positions and dwell—all without loss of energy and accuracy in microns. The Komatsu H1F servo press delivers nearly 3 times more working energy than a conventional mechanical press – but consumes over 30% less electrical energy! The H1F series is also available in solid frame design (“O” frame) for applications where angular deflection is critical. In capacities from 39 to 220 tons, the H1F presses are in stock and ready for immediate delivery. Schedule a die tryout today!
The H1F Servo -driven Press
Designed for Superior Flexibility and Accuracy
- Ideal for progressive, transfer or manual die operations
- Incorporates modern, state of the art A.C. servo technology into mechanical stamping press designs
- Ability to control slide velocity throughout the stamping work being done-optimal slide motion can be set for any application
- Maintains constant working energy throughout stroke regardless of slide velocity
- Provides ability to dwell at position to allow timing of secondary work within the press cycle time
- Improved part quality
- Increased die life
- Ability to program multiple motion paths before returning to top dead center
- Automatically maintain and adjust slide position to assure consistent die height
- Elimination of high maintenance mechanical components like the clutch-brake unit
- Reduces importance of die or part lubrication
- Reduces die tryout time and expense
- Saves energy cost by reducing electricity consumption
A Higher Level of Standard Equipment for Increased Performance
- U.S. standard bolster and slide machining
- Heavy plate, rigid frame construction
- Available in optional solid side-frame design on 45-ton models and above
- Pre-machined, heavy-duty cast slide with adapter plates on 80-ton models and above
- Precision plunger guide design
- Precision oil-lubricated long 6-point gibs
- Automatic lubrication of main drive components
- Quick-responding, dependable hydraulic overload protector
- Shock-resistant, pendant mounted control
- T-stand for easy set-up and operation
- Job storage memory
- Safety block with interlock
- Air counter-balance system
Standard Features
Standard Features
Drive Layout
Komatsu Engineering has combined today’s modern A.C. servo technology with its proven and very rigid toggle linkage from our forging presses to provide a versatile, efficient and reliable solution to the changing demands of today’s pressroom. Incorporating a series of mechanical ratios allows for a standard motor size from a proven motor and control system – no proprietary motors or motor controller are used.
Accuracy Within Microns
A Linear Glass Scale is mounted to the frame of the press and monitors the slide position to assure repeatable die height consistency at the bottom of the stroke where the work is being done. The linear scale is mounted to a sub-frame, fixed at the bottom to assure slide position accuracy and allowed to “float” at the top while the press frame is under load.
Auto Die Height Adjustment
The press control continuously monitors the slide position to assure consistent part quality. Die height adjustments are automatically made during continuous operation of the press. System reliability is assured by constant position monitoring of the main shaft angle detector, motor encoder and actual slide position by the linear scale.
Plunger Guide System
Designed for high precision and less die wear. Thrust load from eccentric motion is absorbed by the plunger guide system. The plunger guide is the primary guiding force, preventing side load on the gibs. A size-specific plunger guide is engineered for each different press model, providing maximum performance for each unit. Komatsu also employs full-length gibs that capture the entire length of the slide guide. Gib tolerances are set to Komatsu’s tolerances of 0.0015″ nom. per gib with oil (not grease) lubrication, allowing them to last up to 200 times longer than conventional gibs. Together, the plunger guide and gib surface area add up to 4-5 times the guiding surface area of our nearest competitors. Less routine gib maintenance, less die wear and higher part accuracy are the positive end result, which can translate into improved profits for you.
Drive System and Control
Komatsu’s unique combination of toggle-linkage and standard AC servo technology allows for a compact and efficient motor size. The dual timing belts are constantly monitored electronically for motion and breakage, isolating the servomotor from direct load and shock inherent to stamping operations.
Hydraulic Overload Protector
Helps prevent damage to the press and dies. All Komatsu presses are equipped with a hydraulic overload protector, a feature that has been standard for decades helping to protect against damage to the press. If the rated load is exceeded, the press stops automatically. Since the hydraulic pressure can be released easily, operations can be resumed smoothly even if jamming occurs.
SIT IV – System Integrated Terminal
Advanced electronics technology provides user-friendly operation and outstanding reliability. The SIT IV electronic press control unit is designed to provide the fastest, easiest, and most reliable control available for all press functions. Included as standard equipment on the Komatsu H1F and H2W presses, SIT IV incorporates all the latest thinking in press control unit design.
Simple Guidance. SIT IV displays operational procedure guidance for select press functions. Intuitive, user-friendly prompts guide press operators in a logical series of steps, for faster, more reliable press set up and operation. The SIT IV pendant is also used for all motion programming. Slide velocity is adjusted in percentage values. When a velocity change is desired, the exact position where this change occurs can be set by actual slide position or in degrees of operation. The slide motion can be programmed to mutliple stages before a complete return to Cycle Start Position (CPS) must occur.
- All information necessary for press set-up, start-up, operation and diagnostics is available in one display, at the touch of a button.
- Language terminology and graphics are user-friendly, easily understood by the press operator in plain view in one control central location on the digital display. Display also includes plain language description of fault messages.
- SIT IV has the ability to integrate with current press room equipment, such as electronic coil feeds.
- Operator “T-Stand” control interface houses all switches and push-buttons required for ordinary press set-up and operation, including Push Buttons for slide adjustment.
- Die Data Recording function can store and retrieve data, including cam and fault detection angle as well as production performance. Also includes digital display of “stored” press speed and actual press speed, plus crank angle.
- Alpha-numeric entry of die name and memo data for easy cataloging and referencing.
- 8.4″ Color Screen
- Built-in Comm. Port for optional V.I.S.
- Digital total Counters
- 1-Production, re-settable
- 1-lot (pre-set), re-settable
- 4 – Electronic rotary cams
- 1 – Pneumatic air ejector with cam
- Mode Selections:
- (1) Off, (2) Inch, (3) Single Stroke, (4) Continuous
- Optional Modes:
- (1) Automatic Single Stroke, (2) Automatic Continuous
- Extensive use of electronics gives outstanding reliability.
- Solid – State Control
- Integrated Circuits are used for all control circuits
- Increased safety, longer operation life and high reliability.
Digital display for improved operation performance. Digital display of the crank angle and electronic angle detectors provide increased accuracy for press operations. Automatic operation setting and die set-up functions are easier and faster for press operators, with precise, reliable settings every time. To protect the integrity of all electronic systems and provide additional safety, monitor lamps indicate defects in circuits of all electronic systems, and faults are detected instantly.
Note – Immediate Stopping Performance Monitor and control reliability. This control meets the current requirements of O.S.H.A. Standards Section 1910.217 and ANSI B11.1
Optional Features
Optional Features
- Electronic Load Monitor (2-channel) – Load monitors are available to continuously monitor loads in all press operations, including blanking, bending, drawing, etc. The monitor also detects die overloads and underloads during operation. In addition, balanced die load is achieved by measuring the off-center-load, thus extending press and die life.
- Vibration Isolating Pads
- Pneumatic Die Cushions
- Emergency Stop Receptacle
- Slide Knockout (mechanical)
- Air Ejector with Cam
- Adjustable Hydraulic Overload
- Coil Line Interface
- Photoelectric Safety Equipment
- Quick Die Change Interface
- Additional set of 4 Electronic Rotary Cams
- Quick Die Equipment
- Hydraulic die clamps available in either lever or cylinder type.
- Hydraulic die lifters.
- Mechanical draw out rails. (note: re-machining of “T” slots may be required)
- V.I.S. Visual Inspection System – Monitor slide motion and velocity, and make adjustments – right from your USB-equipped laptop or PC! (Note – Load Monitor Required)
Warning – For protection of the operator, point of use guards should be used at all times. Komatsu presses do not include O.S.H.A. recommended point of protection guards.
Automation – Complete turn-key Komatsu designed press systems including coil lines, die carting and systems engineering tailored to your specific application.
Catalog and Specs
Catalog and Specs
Komatsu Warranty
The Komatsu Warranty
When a press is designed as a system, it should be expected to perform as a system without routine tear downs for wear items (the conventional “weak link” in our competitors’ presses.) That’s why every Komatsu Press comes with a Two Year Unconditional Warranty on anything that rolls, slides or moves – parts and labor. Unlike other manufacturers, there is no hourly limit – your press is guaranteed to perform 3 shifts a day, 7 days a week, 365 days a year. With Komatsu systems engineering it’s possible to extract the full potential from your press, and the full revenue potential from every job.